Alloy steel pipes have good hardness, which are widely used for pipelines for transporting oil, natural gas, gas, water and certain solid materials. The common alloys are ferroalloys, ferro-chromium alloys, iron-nickel alloys, aluminum alloys(light weights) and copper alloys(good thermal conductivity). The main materials include 16-50Mn, 27SiMn, 20-40Cr, 12-42CrMo, 16Mn, 12Cr1MoV, T91, 27SiMn, 30CrMo, 15CrMo, 20G, Cr9Mo, 10CrMo910, etc. Alloy steel pipes made from 16Mn belong to low alloy steel pipes.
Applications of alloy steel pipes
Alloy steel pipes are mainly used for high-pressure and high temperature pipelines and equipment such as power plants, nuclear power, high-pressure boilers, high temperature superheaters and reheaters.
Three expressions of alloy steel pipe specifications
Specific welding steps of alloy steel pipes
Welding processes of alloy steel pipes are heating before welding, quenching and tempering after welding.
Heating
Before welding the alloy steel pipe, it should be heated, and weld it after the temperature is controlled for 30 minutes. The heating and virtual beam temperature tempering of welding are actively operated by the temperature control cabinet for temperature adjustment. Adopt far infrared tracking heat treatment furnace plates. Intelligently and actively set the graph and record the graph, and use the thermal resistance to accurately measure the temperature. The thermal resistance measuring point is from 15mm to 20mm away from the edge of the weld during heating.
Welding methods
1. In order to prevent welding deformation of the alloy steel pipe, each column joint is welded symmetrically by two people, and the welding direction is from the middle to the two sides. After welding one to three layers, reverse planing should be carried out. After the carbon arc gouging is used, the welding equipment needs to be polished. The welding surface should be nitridation treated to show the metal texture and prevent the surface carbonization from causing cracks. The outer hole is welded once, and the remaining inner holes are welded once.
3. The welding current, welding speed and number of overlapping layers of multiple welding machines should be maintained.
4. In welding, you must start welding from the pilot arc board and finish welding on the pilot arc board. Cut, polish and clean after welding.
Quenching and tempering after welding
After the seam are welded, it should be tempered within 12 hours. If the alloy steel pipe cannot be quenched and tempered immediately, heat preservation and slow cooling should be adopted. When the alloy steel pipe is tempered, temperatures of the two thermal resistances should be measured and the thermal resistance should be welded on both sides of the seam.
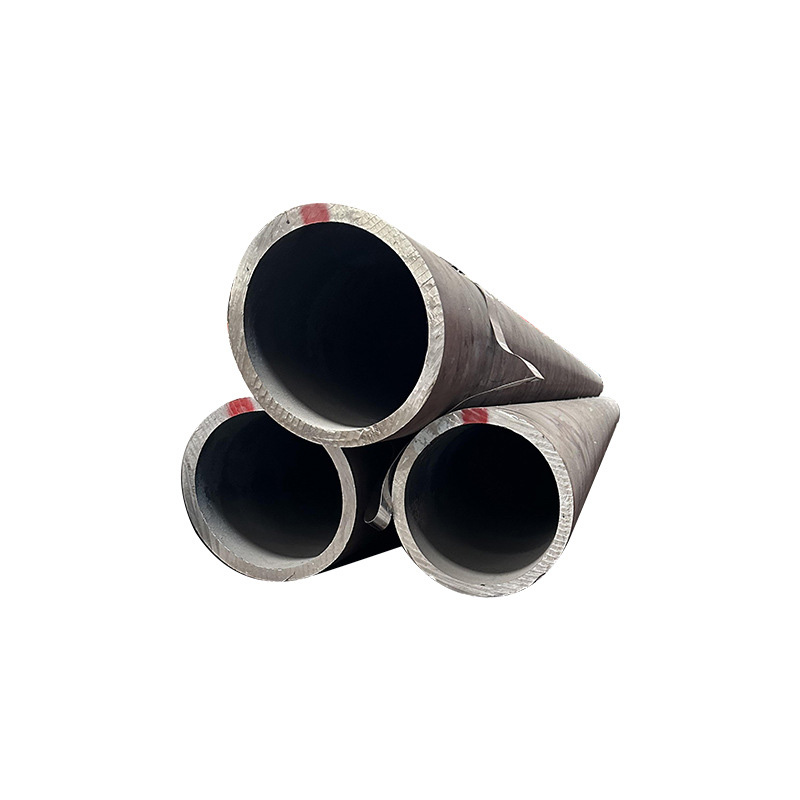